Контроль качества в машиностроении — это критически важный аспект, который напрямую влияет на успех производства и удовлетворенность клиентов. Без надежных методов проверки качество продукции может значительно пострадать, что приведет к потере доверия и финансовым потерям.
Особое внимание уделяется не только итоговой проверке изделий, но и каждому этапу производственного процесса. Это включает в себя контроль проектирования, производство и даже логистику. Применение передовых технологий, таких как автоматизированные системы контроля и аналитика больших данных, поможет минимизировать ошибки и улучшить общее качество продукции.
Однако, технологии — это не единственный ключ к успеху. Человеческий фактор играет значительную роль в управлении качеством, так как навыки и профессионализм работников напрямую влияют на конечный результат. Каждый сотрудник должен быть вовлечен в процесс, понимая его значимость для всего предприятия.
Изучение и внедрение новых методов и инноваций в области контроля качества позволяют компаниям оставаться на шаг впереди в условиях постоянно меняющихся рыночных требований и ожиданий клиентов.
- Введение в контроль качества
- Историческая справка и развитие стандартов
- Методологии и подходы
- Технологии и инструменты контроля
- Роль человеческого фактора
- Будущее и инновации в контроле качества
Введение в контроль качества
В современном мире контроль качества стал неотъемлемой частью любого производственного процесса, особенно в машиностроении. Здесь все начинается с четкого понимания, что такое качество и как его можно измерить. Контроль качества представляет собой систему мер, направленных на обеспечение соответствия продукции стандартам качества на всех стадиях производственного процесса. Это не просто проверка готового изделия, это комплексный подход, который охватывает проектирование, разработку, производство и поставку. Главная цель — уменьшение количества дефектов и повышение надежности продукции.
История контроля качества насчитывает не одно десятилетие, и этот процесс значительно эволюционировал. В 1920-х годах Уолтер Шухарт впервые представил концепцию статистического контроля качества, которая стала основой для дальнейшего развития дисциплины. Сегодня контроль качества включает в себя не только статистику, но и такие методологии, как шесть сигм и lean, обеспечивая более точный и систематический подход к управлению качеством в машиностроении.
"Качество означает делать это правильно, когда никто не смотрит" — Генри Форд.
Современные технологии оказали огромное влияние на контроль качества. Компании используют сложные программные решения для анализа данных о производственном процессе, что позволяет выявлять потенциальные проблемы на самых ранних стадиях. Важную роль играет и человеческий фактор, поскольку профессионализм рабочих и инженеров оказывает непосредственное влияние на результат. Это значит, что без систематического обучения и вовлеченности персонала, достичь высокого уровня качества будет крайне сложно.
Ключ к успешному управлению качеством заключается также в интеграции новых технологий и процедур. Практики аудита качества, в том числе внутреннего и внешнего, стали стандартом успешной работы большинства предприятий. Эти аудиты позволяют не только подтвердить соответствие продукции требованиям, но и определить области, требующие улучшений. Компании, которые уделяют должное внимание управлению качеством, добиваются не только значительных экономических преимуществ, но и укрепляют свою конкурентоспособность на мировом рынке.
Историческая справка и развитие стандартов
Понимание истории контроля качества в машиностроении помогает оценить её влияние на современное производство. Начать, пожалуй, стоит с первых образцов промышленной революции в 18 веке, когда массовое производство только начинало развиваться. В те времена даже наличие стандартов как таковых было редкостью. Однако с увеличением объемов производства возникла потребность в унификации процессов и проверки продукции. Это послужило толчком к разработке первых механизмов контроля качества.
Переходя в начале 20 века, управление качеством стало более систематическим. Многие компании осознали, что качество — это не просто функция последующего инспектирования, а критически важная часть производственного процесса. Этот период ознаменовался развитием научного менеджмента, где особую роль сыграли работы инженеров как Генри Ганта и Фредерика Тейлора, создавших первые инструменты для оценки эффективности производительных процессов. Тогда же родилось понятие статистического контроля качества, благодаря трудам таких ученых как Шухарт.
После Второй мировой войны развитие контроля качества получило новый импульс, особенно в Японии. Страна воплотила идею тотального управления качеством (TQM) с акцентом на постоянное улучшение и вовлечение каждого сотрудника в процесс. Японские компании показали, что интеграция всех аспектов управления качеством позволяет не только улучшать продукты, но и экономить значительные ресурсы. Это положительно сказалось на их позиции на глобальном рынке.
"Качество — это бесплатное вложение. Оно всегда окупается", — однажды заметил Эдвард Деминг, известный эксперт в области управления качеством. Его работы показали, что улучшение качества напрямую связано с экономической выгодой и конкурентоспособностью.
Спустя десятилетия становления, международные стандарты ISO стали маяком для компаний по всему миру, направляя производственные процессы в единое русло. Сегодня стандарт ISO 9001 является отправной точкой для большинства предприятий, стремящихся улучшить свои системы менеджмента качества. Эти стандарты обеспечивают общий язык и инструментарий, чтобы предприятия могли обмениваться знаниями и опытом, а также выстраивать работу таким образом, чтобы минимизировать производственные ошибки и увеличивать свою эффективность.
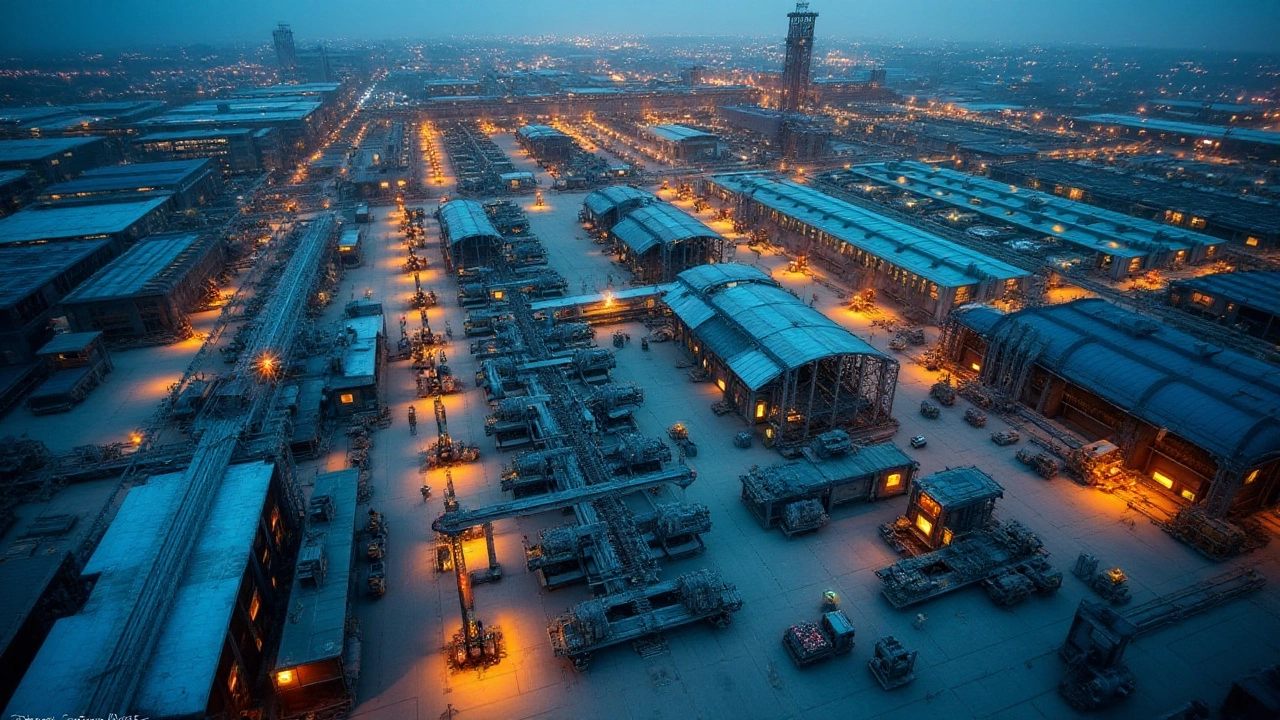
Методологии и подходы
В современном машиностроении подходы к контролю качества играют ключевую роль в обеспечении надежности и соответствия продукции высоким стандартам. Существует множество методологий, каждая из которых имеет свои особенности и область применения. Одной из наиболее популярных является методология Six Sigma, которая зародилась в компании Motorola в 1980-х годах. Эта методика нацелена на минимизацию дефектов и отклонений в любых бизнес-процессах, включая производственные. Она базируется на строгом статистическом анализе и постоянном совершенствовании процессов.
Также нельзя не упомянуть о методе Lean, который использовался, чтобы сократить затраты и улучшить качество за счет исключения всех форм потерь и неэффективностей. В основе Lean лежит принцип создания ценности для клиента и минимизации операций, которые не приносят его непосредственно. Эти два подхода часто объединяются в Lean Six Sigma, что позволяет одновременно улучшать производственные процессы и поддерживать их стабильность на самом высоком уровне.
Другим важным подходом являются концепции Всеобщего управления качеством (TQM), которые акцентируют внимание на ответственности каждого сотрудника за качество конечного продукта. TQM предполагает вовлечение всех уровней иерархии компании в процессы планирования и осуществления улучшений. Это создает культуру, ориентированную на качество, где каждый член команды понимает важность своей роли в производственном процессе.
Использование современной технологии в контроле качества также отражено в методах, связанных с автоматизацией и AI-инструментами. Системы машинного обучения способны анализировать огромные массивы данных и предугадывать потенциальные сбои, до того как они произойдут. Особенно полезны эти технологии на этапе прогнозирования и контроля за оборудованием.
Известное изречение от Эдвардса Деминга, отца современного контроля качества: "Качество - это не конечный пункт назначения, а постоянный процесс совершенствования."
Одним из более недавних инструментов стала концепция Индустрии 4.0, включающая в себя использование интернет-технологий и интернета вещей для повышения точности и эффективности контроля качества. Это позволяет компаниям в реальном времени отслеживать состояние оборудования и продукции, внося коррективы на лету для предупреждения ошибок. Все вышеописанные методы и подходы интегрируются в современное машиностроение с использованием IT-технологий, создавая мощный инструментарий управления качеством.
Технологии и инструменты контроля
Современные технологии в области контроля качества кардинально изменили подходы к проверке продукции в машиностроении. Внедрение автоматизированных систем контроля позволило предприятиям значительно повысить точность и скорость оценки изделий. Одним из таких достижений стало использование роботизированных устройств, которые могут проводить инспекцию деталей с высокой степенью детализации и без участия человека. Это существенно сокращает время на проверку и уменьшает вероятность человеческого фактора, который может повлиять на результат анализа.
Другим не менее важным инструментом является анализ больших данных. Собирая и обрабатывая информацию с множества сенсоров и устройств, компании получают возможность более точно прогнозировать потенциальные неисправности и улучшать свои производственные процессы. Благодаря этим данным руководители могут принимать более обоснованные решения, а инженеры – оперативно вносить изменения на производственных линиях.
Фокус также делается на внедрение технологий интернета вещей (IoT), где машины и устройства связаны между собой и могут обмениваться информацией в реальном времени. Это расширяет возможности надзора и оперативного вмешательства, предотвращая неисправности еще до их возникновения.
«Внедрение IoT в машиностроении позволяет сократить простои оборудования на 30% и увеличить производительность минимум на 20%», — отмечает известный аналитик в области промышленности.
Важную роль в управлении качеством играет использование неразрушающего контроля, где проверка осуществляется без повреждения исследуемой детали. Ультразвуковые тесты и рентгенография — популярные методы этой категории, которые позволяют выявлять скрытые дефекты в материалах и сварных швах. Эти методы особенно полезны при работе с дорогими материалами, где ошибка может стоить очень дорого. В результате применение подобных методов минимизирует риск бракованных партий и оптимизирует затраты.
Для повышения эффективности и снижения ошибок, многие компании используют системы управления качеством (QMS), которые интегрируют все процессы контроля в единую платформу. Данные системы автоматически отслеживают и анализируют ключевые показатели качества, позволяя быстро выявлять тенденции и узкие места в производстве. Таким образом, контроль качества становится более прозрачным и управляемым.
Не стоит забывать о важности обучения персонала, работающего с этими технологиями. Доступ к современным инструментам контроля без знаний и навыков их использования может оказаться бесполезным. Поэтому компании активно инвестируют в обучение своих сотрудников, чтобы они могли максимально эффективно использовать все технические возможности. Применение новых знаний на практике способствует повышению общей эффективности и качества работы.
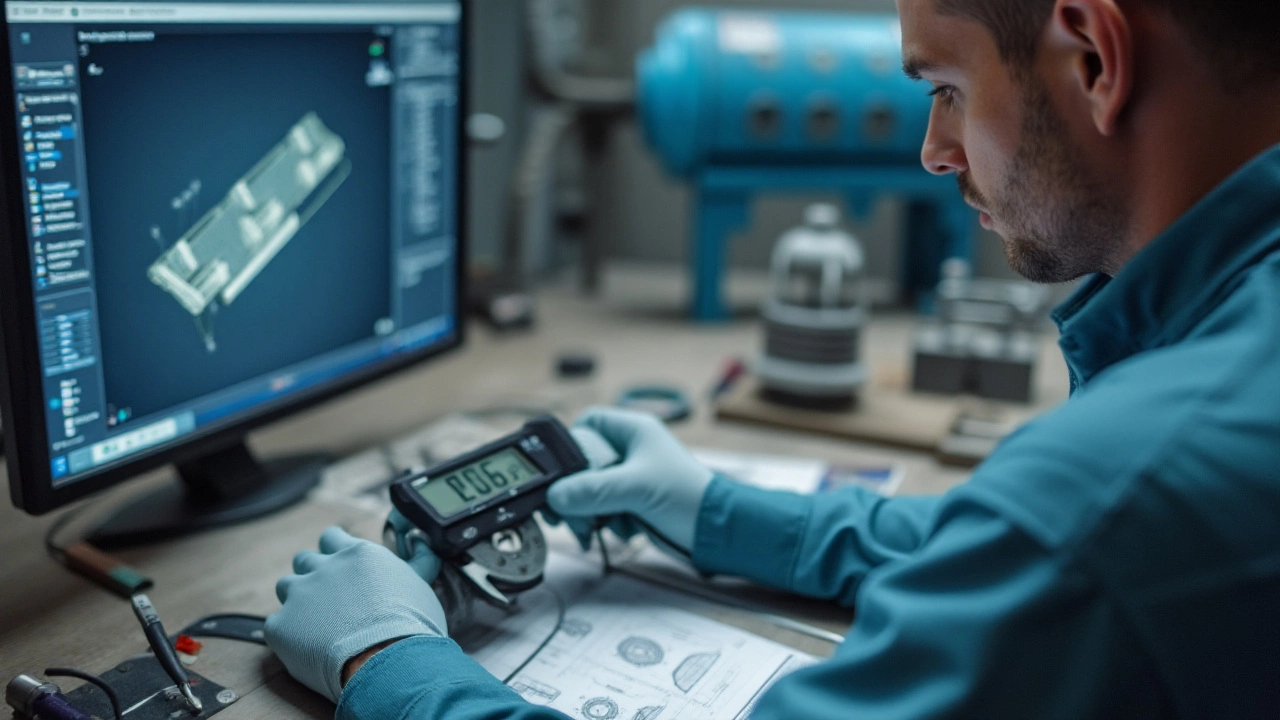
Роль человеческого фактора
В машиностроении, как и в любой другой сложной отрасли, человеческий фактор играет решающую роль в контроле качества. Хотя современные автоматизированные системы и способны выполнять множество задач с большой точностью, именно благодаря людям вводятся инновации, развиваются новые стандарты и принимаются уникальные инновационные решения. Работники проводят первичные и вторичные проверки, анализируют результаты и принимают окончательные решения по качеству продукции.
Человеческий фактор не ограничивается только специалистами по контролю качества. Машиностроение требует, чтобы все участники процесса, начиная от проектировщиков и заканчивая операторами машин, понимали важность качества и были вовлечены в его поддержание. Это взаимосвязь всех элементов, от руководящих должностей до рядовых сотрудников, которая поддерживает культурную приверженность качеству продукции в компании. Особенно важно подготавливать сотрудников с учетом новейших технологий и методов.
Компании, которые уделяют внимание человеческому фактору, инвестируют в обучение и развитие своих сотрудников, добиваются более высоких результатов. Широкое распространение получает практика обмена опытом и знаниями среди работников, что способствует не только повышению квалификации, но и улучшению морального духа внутри коллектива. Мотивация и вовлечение сотрудников напрямую влияют на эффективность контроля качества.
По данным исследования McKinsey, компании, внедряющие программы по развитию персонала и усилению роли человеческого фактора в контроле качества, снижают риск производственных дефектов на 25%.
Управление качеством существенно зависит от того, насколько персонал осведомлен о последних изменениях в стандартах и технологиях. Профессионалы, обладающие богатым опытом, часто делятся знаниями с менее опытными сотрудниками, что способствует быстрому распространению лучших практик внутри команды. Благодаря такой интеграции всестороннего опыта и понимания процессов качество продукции сохраняет на должном уровне даже в условиях высокой конкуренции и быстро изменяющихся потребностей рынка.
Человеческий фактор в контроле качества — это не только навыки и умения, но и способность принимать адекватные решения в стрессовых ситуациях, а также выявление и анализ ошибок для их оперативного устранения. Этот аспект играет особенно важную роль при внедрении новых технологий и процессов, когда необходима гибкость мышления и быстрая реакция на изменения в производственной среде.
Будущее и инновации в контроле качества
Заглядывая в будущее, становится ясно, что контроль качества в машиностроении претерпит значительные изменения. Это связано с бурным развитием технологий и внедрением новых подходов в управление производственными процессами. Одной из ключевых тенденций является интеграция искусственного интеллекта (ИИ) и машинного обучения. Эти инструменты способны анализировать огромные объемы данных в реальном времени, позволяя выявлять дефекты на ранних стадиях и предлагать эффективные решения по их устранению. Это значительно сокращает время на устранение проблем и позволяет избегать массового брака продукции.
Еще одной перспективной областью являются блокчейн-технологии, которые начинают применяться для обеспечения прозрачности и надежности данных о качестве продукции на всех этапах производственной цепочки. Применение блокчейна помогает проследить происхождение и историю производства каждой детали, что важно для оптимизации производственного процесса и повышения доверия клиентов.
Автоматизация и роботизация
Скоростной прогресс в автоматизации и роботизации также меняет ландшафт управления качеством. Роботы не только заменяют человека на рутинных и опасных работах, но и обеспечивают высокую точность при проверке изделий. Например, автоматические инспекционные системы, оснащенные камерами высокого разрешения и датчиками, способны обнаруживать микротрещины, отсутствие или дефекты деталей без участия человека. Это способствует увеличению производительности и снижению затрат.
"Искусственный интеллект и автоматизация - это будущее контроля качества, их внедрение позволит поднять процент точности выявления дефектов до максимально возможного уровня", — отметил эксперт из 'Международного института управления качеством'.
Ценность данных
С увеличением объемов производственных данных особую актуальность приобретает аналитика больших данных. Используя современные аналитические платформы, компании могут создавать подробные отчеты и прогнозы, применяя их для улучшения процессов и повышения эффективности. Это обеспечивает более гибкое и быстрое реагирование на изменения рынка, а также улучшает взаимодействие со снабженцами и покупателями. Важно понимать, что в ближайшие годы компании, способные эффективно использовать данные для оптимизации контроля качества, будут иметь преимущество на рынке.
Таким образом, машиностроение вступает в новую эру, когда технологии играют ведущую роль в обеспечении непрерывного совершенствования качества продукции. Грамотно используя инновации, компании могут не только соответствовать современным стандартам, но и задавать новые ориентиры для всей индустрии.
Оставить комментарий