Фраза «промышленная автоматизация» часто звучит как нечто отдалённое и сложное, но спроси любого инженера на производстве — и ты услышишь массу историй как о катастрофах из-за перегрева конвейера, так и спасительных ситуациях, когда «умная» система выдала тревогу раньше человека. Автоматизация на промышленном уровне проникла не только на заводы и фабрики — без неё сложно представить энергетику, химию, пищевую отрасль или транспорт. И тут речь идёт не просто о роботах, монотонно собирающих детали или фасующих упаковки. Это целая вселенная взаимосвязанных решений, платформ и протоколов, где человек чаще выступает наблюдателем и стратегом, чем непосредственным исполнителем.
Что такое промышленный уровень автоматизации и зачем он нужен?
Начать стоит с вопроса: как отличить бытовую автоматику — например, чайник с таймером — от промышленной? Промышленный уровень автоматизации — это масштаб, когда ошибочная команда может остановить тысячу линий, а удачное решение обернётся миллионными экономиями и безопасностью. Всё строится вокруг систем управления, которые координируют работу оборудования, обеспечивают сбор и анализ данных, предотвращают аварии и делают производство прогнозируемым и стабильным.
В промышленности уже к 2025 году доля автоматизации в мировом производстве перевалила за 60% (по данным Statista), а по прогнозам консалтинговой компании McKinsey, предприятия, внедрившие цифровые системы управления, как правило сокращают производственные издержки на 20-30%. Такой подход невозможен без чёткого понимания, из чего складывается технологический фундамент:
- Промышленные контроллеры (ПЛК) — мозг автоматизации. Это не просто мини-компьютеры, а центры принятия решений: отслеживают, когда нужно запустить насос, выключить станок, отследить брак или подать сигнал аварии.
- Датчики и исполнительные механизмы — глаза и руки автоматизации. Без сенсоров невозможно точно понимать текущую температуру, давление, влажность, или даже вибрации подшипника.
- Сети передачи данных — жизненно важная артерия. Промышленные Ethernet-сети и беспроводные протоколы позволяют связывать все участки цеха или даже разных заводов в единую систему, где каждый датчик — источник ценной информации.
- Системы человеко-машинного интерфейса (HMI/SCADA) — делают сложные данные понятными для оператора: графики, аварийные сигналы, статистика в реальном времени.
Особенность современного промышленного уровня — интеграция с ERP-системами, логистикой, энергетикой и даже со складскими и торговыми платформами. Этот конструктор сегодня способен охватить все этапы: от поступления сырья до контроля отгрузки готовой продукции.
Интересный факт: на производстве «Audi» в Германии внедрена система адаптивного управления на базе искусственного интеллекта. Она анализирует данные со 1500+ датчиков и способна регулировать логистику, учитывая не только движение техники, но и наличие комплектующих в реальном времени. Экономия времени — до 30% на отдельных операциях (источник: официальный пресс-релиз компании Audi, 2024).
Многие компании делят уровни автоматизации на шесть больших диапазонов: от физического контроля до управления предприятием на уровне бизнеса. Такой подход принят, например, в модели ISA-95 (международный стандарт интеграции производства и информационных систем).
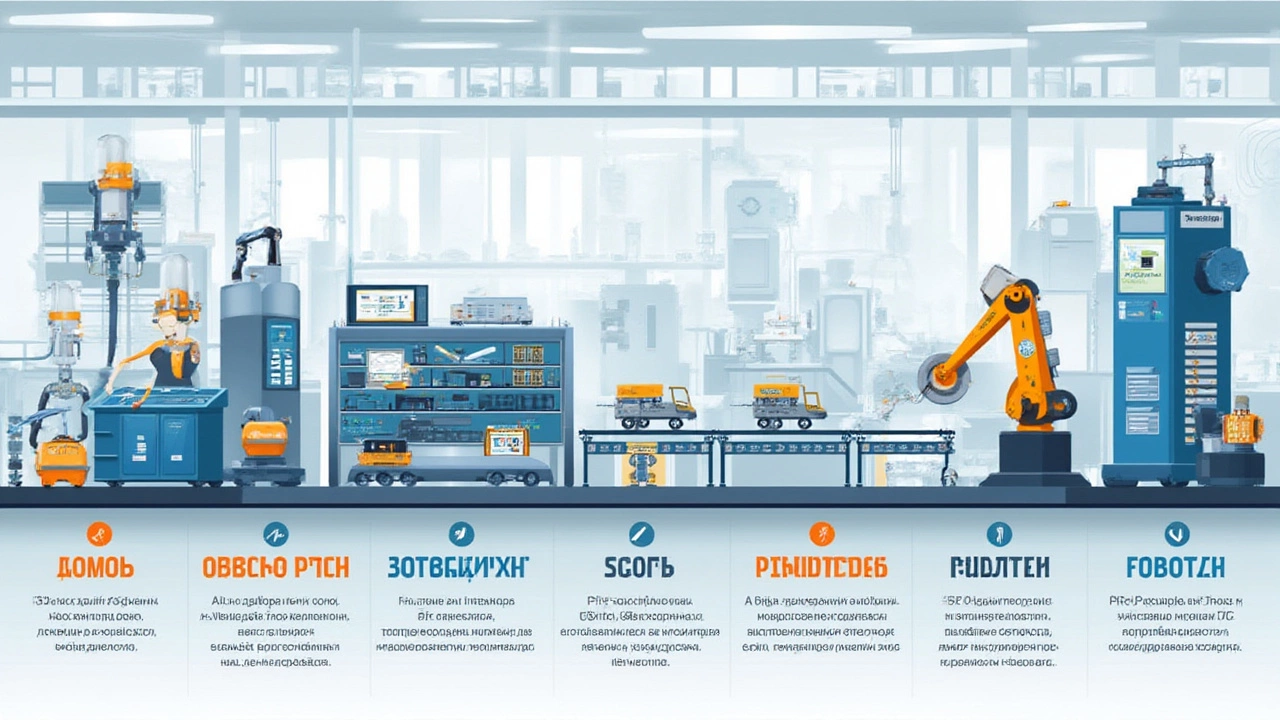
Ключевые компоненты и уровни промышленных автоматизированных систем
Промышленная автоматизация складывается из нескольких чётко взаимодействующих блоков. Иногда их называют уровнями, иногда контурами — суть одна: каждый элемент работает на общий результат.
- Поле устройств (Field Level): Настоящий физический мир — датчики, клапаны, реле, моторы. Всё, что может измерять, щёлкать, открывать или закрывать. Реальные примеры? Датчик давления на нефтепроводе или приводы на воротах склада.
- Управляющий уровень (Control Level): Сердце управления — программируемые логические контроллеры (ПЛК/PLC), микроконтроллеры, распределённые системы управления (DCS). Они принимают решения на основе сигналов с «поля» и передают команды исполнительным устройствам.
- Мониторинг и диспетчеризация (Supervisory Level): Системы SCADA и HMI. Позволяют персоналу видеть происходящее, реагировать на сбои, собирать данные для дальнейшего анализа.
- Информационный/Управленческий уровень (Information/Enterprise Level): ERP, MES и другие платформы, которые объединяют производственные и бизнес-процессы, помогают планировать, учитывать ресурсы, оптимизировать производство в целом.
Слабое место любой сложной системы — несовместимость между уровнями и брендами оборудования. Поэтому в промышленности ключевой тренд последних лет — открытые стандарты и протоколы (Modbus, OPC UA, Profinet и другие), которые позволяют собирать в один «купол» оборудования разных производителей. Ещё лет десять назад казалось фантастикой интегрировать китайский частотник и немецкий контроллер в одну сеть без дополнительных танцев с бубном.
Стоит упомянуть такие решения, как кибербезопасность в автоматизации: после громких атак типа Stuxnet заводы стали закрывать доступ к ключевым сегментам управляющих сетей, использовать отдельные серверы для SCADA, внедрять двухфакторную аутентификацию даже при входе в локальную сеть. «Доверие — это хорошо, но резервный план на случай сбоя лучше», — однажды сказал специалист Siemens на отраслевом семинаре.
Чтобы система реально оправдала своё название, важно регулярно проводить обслуживание, обновление прошивок, тестировать аварийные сценарии и обучать сотрудников работе с новыми платформами. Автоматизация не отменяет человеческий фактор — она делает его более управляемым и предсказуемым.
В некоторых отраслях (химия, фармацевтика) контроль качества и документация автоматически генерируются на основе данных «по факту», исключая влияние человеческой ошибки. Например, на заводе Pfizer за сутки фиксируется и архивируется до 10 ТБ данных о каждом этапе производства — это позволяет быстро выявить причину брака даже спустя месяцы после производства очередной партии.
Совет для практиков: не стоит слепо автоматизировать процессы ради моды или красивого отчёта. Настоящий профит начинается, когда автоматизация решает конкретную боль — помогает избежать аварий, снижает расходы на сырьё, или ускоряет выпуск продукции.
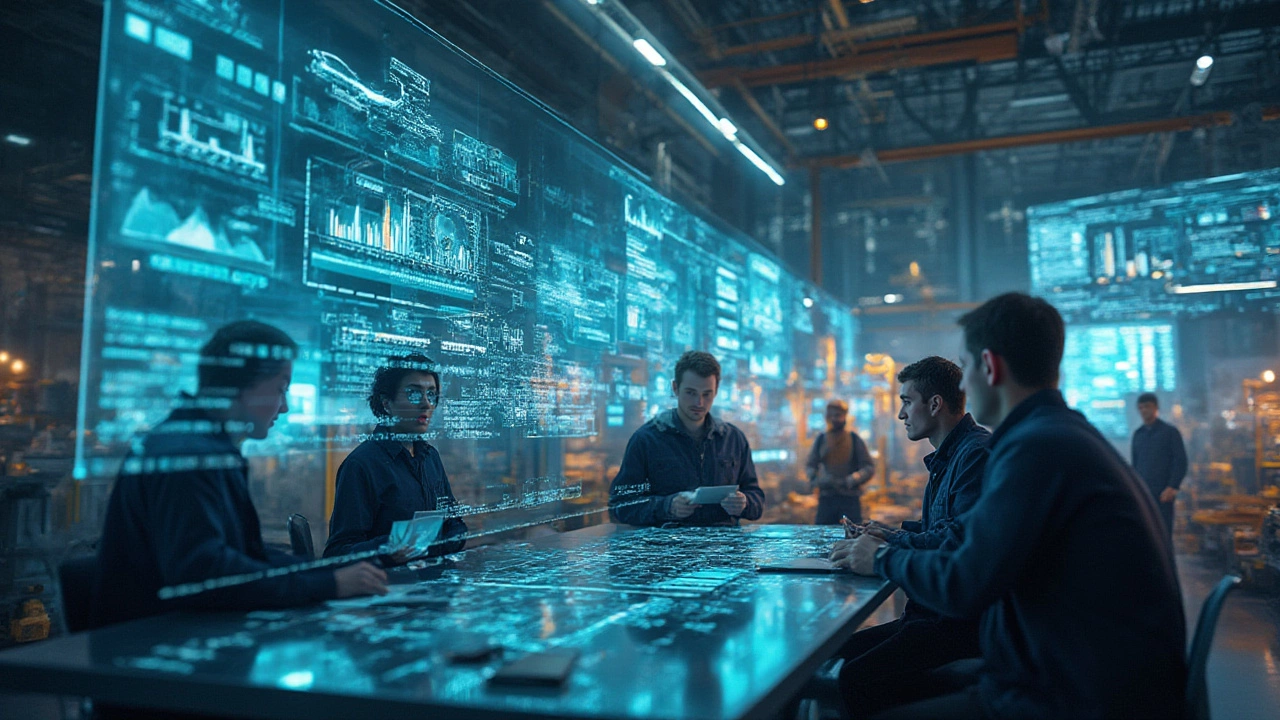
Современные тренды и ошибки при внедрении автоматизации на производстве
В 2025 году автоматизация уже не воспринимается как роскошь — речь идёт о необходимости быть конкурентоспособным. Тем не менее, колоссальные бюджеты иногда улетают «в молоко» по банальным причинам: непонимание задач, отсутствие чёткого ТЗ, неграмотная интеграция новых решений с «ветеранами» производства, или просто игнорирование человеческого фактора.
Ключевой тренд — переход к интеллектуальным системам. Многие современные платформы уже используют искусственный интеллект для предиктивной диагностики: пока обычный датчик просто сигнализирует о поломке, интеллектуальная система может предсказать износ детали и запланировать ремонт без остановки всей линии. В 2024 году компания Schneider Electric сообщила, что средний срок до отказа оборудования у их клиентов благодаря предиктивной аналитике увеличился на 40%.
Ещё один тренд — удалённый мониторинг: цифровые двойники, работающие на облачных платформах, позволяют руководителю увидеть, что происходит в производстве даже с телефона в самолёте. По данным ABB, около 70% новых промышленных проектов в Европе в 2025 году уже предусматривают дистанционное управление основными производственными объектами.
Реальные ошибки? Первая — попытки внедрить автоматизацию сверху вниз, игнорируя мнение производственников или специалистов, знакомых с текущими процессами. Вторая — экономия на обучении. Новые технологии быстро устаревают, если люди боятся их использовать или не могут диагностировать сбои. И третья — отсутствие резервирования: если резервный сервер не протестирован вовремя, сбой в самый неожиданный момент может остановить работу на часы.
Совет: любую систему строят не ради самой системы, а для решения конкретной задачи. Всегда задавайте себе вопрос: какой результат принесёт автоматизация — ускорение, экономию, повышение безопасности, сокращение брака?
В мире уже внедряют практики виртуальной и дополненной реальности для обучения операторов, тестируют автоматизированные склады с самостоятельным управлением AGV-роботов (например, на заводах Tesla), и даже создают гибкие производственные линии, которые можно быстро «перекроить» под новый продукт за счёт софт-связанных машин и модульных решений.
Не забывайте: «Автоматизация — не самоцель. Она работает только тогда, когда отвечает на реальные вызовы бизнеса», — как сказал аналитик консалтинговой компании Deloitte на форуме в Дюссельдорфе, 2025.
Оставить комментарий