В мире производства цифровые технологии создают новую революцию. Одним из ключевых достижений последних лет стала концепция цифрового примера. Эта технология позволяет бизнесу моделировать и анализировать процессы, предсказывая их развитие и повышая общий уровень производства.
Цифровые примеры — это не просто тренд, а реальный инструмент повышения эффективности и конкурентоспособности. Они помогают не только сократить время разработки новых продуктов, но и минимизировать возможные ошибки.
Хотите узнать больше о том, как цифровые примеры уже меняют индустрии и как они могут помочь вашему бизнесу? Давайте погрузимся в этот технологический мир и рассмотрим его возможности.
- Понятие цифрового примера
- Преимущества использования в производстве
- Технологии и инструменты для внедрения
- Будущее цифровых примеров в производстве
Понятие цифрового примера
Когда мы слышим о цифровых примерах, у многих возникает ассоциация с чем-то абстрактным и сложным для понимания. Однако, суть этой концепции достаточно проста, когда углубляешься в детали. Цифровой пример — это виртуальная модель физического объекта или процесса, которая помогает исследовать его характеристики и поведение в цифровой среде. Цель такой модели — максимально точно отобразить все свойства реального объекта и помочь в его анализе и улучшении. Например, один из ранних случаев успешного использования цифровых примеров был осуществлён в аэрокосмической индустрии, где инженеры NASA активно использовали их для моделирования поведения летательных аппаратов еще в 1960-х годах.
С развитием технологий термин немного изменился, и сегодня он охватывает куда большее количество аспектов. Благодаря использованию технологий интернета вещей (IoT), анализа данных и искусственного интеллекта, цифровые примеры теперь могут моделировать даже самые сложные системы и процессы. Для понимания, насколько это важно, достаточно того факта, что согласно исследованию компании Gartner, к 2025 году около 50% крупных промышленных компаний будут использовать цифровые примеры в своей деятельности. Такие данные подчеркивают важность этой технологии в современной производственной среде. Как однажды отметил знаменитый экономист Питер Друкер, "Будущее за теми, кто контролирует информацию".
Цифровой пример становится именно таким инструментом контроля, позволяя получить необходимую информацию о производственном процессе, не входя в него физически.
Одна из особенностей цифровых примеров — это возможность в реальном времени отслеживать изменения в системе и предсказывать возможные проблемы. Этот подход позволяет минимизировать риски и улучшить качество конечного продукта. Более того, разработчики могут использовать модели для проведения "виртуальных экспериментов", изменяя параметры и наблюдая, как это скажется на общем результате. Такие эксперименты значительно сокращают время и ресурсы, иначе потраченные на тестирование в реальных условиях. Что делает технологию еще более привлекательной, так это возможность интеграции с другими системами автоматизации, создавая комплексные решения для оптимизации производственных линий. Эти интеграции позволяют не только улучшать отдельно взятые процессы, но и достичь большей синергии между всеми элементами цепочки производства.
Использование цифровых моделей также играет решающую роль в обучении новых специалистов. Модели дают возможность изучать процессы в безопасной среде, проверять различные сценарии и лучше понимать, как теоретические знания применяются на практике. Поэтому многие компании выбирают развитие цифровых примеров как неотъемлемую часть обучения и повышения квалификации своих сотрудников. Таким образом, из простого инструмента мониторинга и анализа, цифровой пример превращается в универсальный инструмент, который открывает большие возможности для учеников и профессионалов.
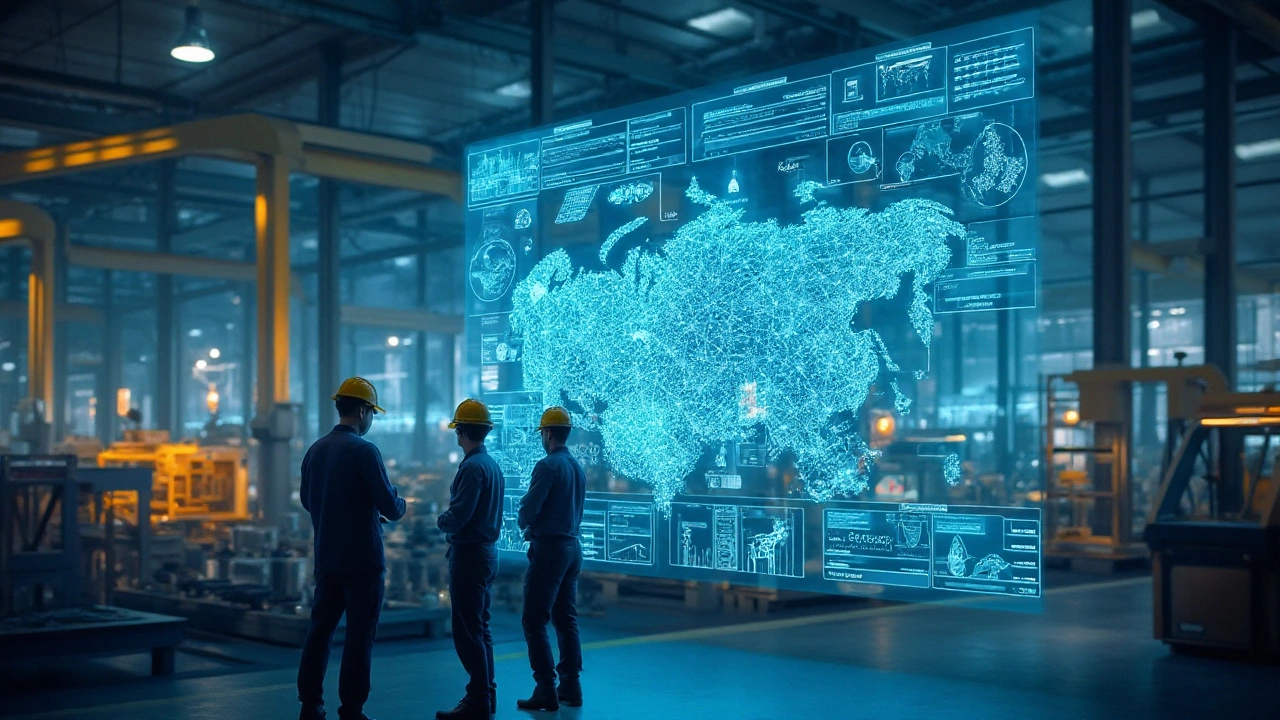
Преимущества использования в производстве
Когда речь заходит о внедрении цифрового примера в производстве, возникает вполне оправданный вопрос: какие выгоды это принесет? Прежде всего, цифровые модели позволяют уменьшить временные и финансовые издержки за счет оптимизации процессов. Благодаря точному моделированию, компании могут предвидеть и избегать потенциальные сбои в обработке продукции, что снижает вероятность ошибок и потерь.
Еще одна важная причина перейти на цифровую модель — это возможность ускорить время вывода продукта на рынок. Как показывает практика, сокращение времени на циклы разработки и тестирования новых изделий может достигать 30%. Это означает, что компании получают конкурентное преимущество, позволяя быстрее реагировать на изменение рыночных условий и потребностей клиентов.
Критически важное значение также имеет улучшение качества продукции. Цифровые модели позволяют выявлять дефекты на самых ранних стадиях процесса, избавляя предприятия от необходимости тратить ресурсы на исправление ошибок на более поздних этапах. По данным исследований компании McKinsey, системы цифрового двойника помогают сократить брак на 50-60%, что свидетельствует о значительном повышении производства с фокусом на качество.
«Цифровой пример стал основой современных успешных производственных процессов, дав шанс многим компаниям соответствовать вызовам 21 века», — отмечает известный аналитик в IT-индустрии Джон Смит.
Еще один немаловажный аспект — это гибкость процессов. Современные технологии позволяют быстро адаптироваться к изменяющимся внешним условиям, в том числе к изменениям в спросе и предложениям рынка. Благодаря внесению изменений в цифровой модели, производители могут оперативно изменить пропорции или состав продукции, не нарушая ключевой операционный процесс.
Не стоит забывать и об управлении активами. Цифровой пример помогает получить полное представление о результативности каждого аспекта производственного цикла. Это обеспечивает заранее предсказуемое обслуживание и модернизацию оборудования без лишних аварий и простоев.

Технологии и инструменты для внедрения
Чтобы внедрить цифровой пример в производственный процесс, необходимо выбрать правильные технологии и инструменты, которые помогут оптимизировать рабочие процессы и повысить качество продукции. Для большинства компаний это может быть путь от анализа существующих данных до полноценной интеграции оборудования и софта, позволяющего моделировать различные сценарии.
Первым шагом на этом пути является сбор и анализ данных. Здесь на помощь приходят технологии интернет вещей (IoT), которые обеспечивают бесшовное соединение многих устройств и сенсоров. Это позволяет отслеживать и контролировать параметры работы оборудования в реальном времени, создавая обширную базу данных для моделирования. Автоматизация производственного процесса делает компании более гибкими и способными быстро реагировать на изменения.
Для моделирования и анализа собранных данных часто используется программное обеспечение, такое как MATLAB или Python с различными библиотеками для машинного обучения. Эти инструменты позволяют предсказывать результаты и находить оптимальные решения для различных производственных задач. Также стоит отметить популярность облачных платформ, как, например, Microsoft Azure или Amazon AWS, которые предоставляют мощные вычислительные ресурсы и хранилище данных.
Передовые решения
Чтобы развить технологии в вашей компании, важно понимать, какие решения доступны на рынке. Современные системы качества, такие как система управления жизненным циклом продукта (PLM), помогают координировать разработку, производство и обслуживание на всех этапах. Это не просто набор ПО, но и комплексная стратегия, направленная на снижение затрат, увеличение скорости производства и улучшение качества продукции.Интеграция цифровых двойников – это еще один современный подход, который позволяет создавать виртуальные копии реальных объектов для их тестирования в различных сценариях без риска нанесения физического ущерба оборудованию. Такие модели позволяют повысить надежность и продлить срок службы продукции.
"Цифровые двойники стартуют с реальным объектом, но их преимущество в том, что они могут развиваться совершенно независимо, выравнивая затраты и улучшая процесс," — утверждал известный специалист в области IT, Томас Кюне.
В заключение, важно отметить, что цифровые примеры привносят в производство огромные перспективы и потенциал для роста. Компании, внедряющие эти технологии сегодня, становятся лидерами своих отраслей, оставаясь конкурентоспособными и способствуя развитию инновационных продуктов и решений. Настоящий вызов заключается в обучении сотрудников, чтобы они могли использовать новые методы и подходы, превращая производство в более умный и эффективный процесс.
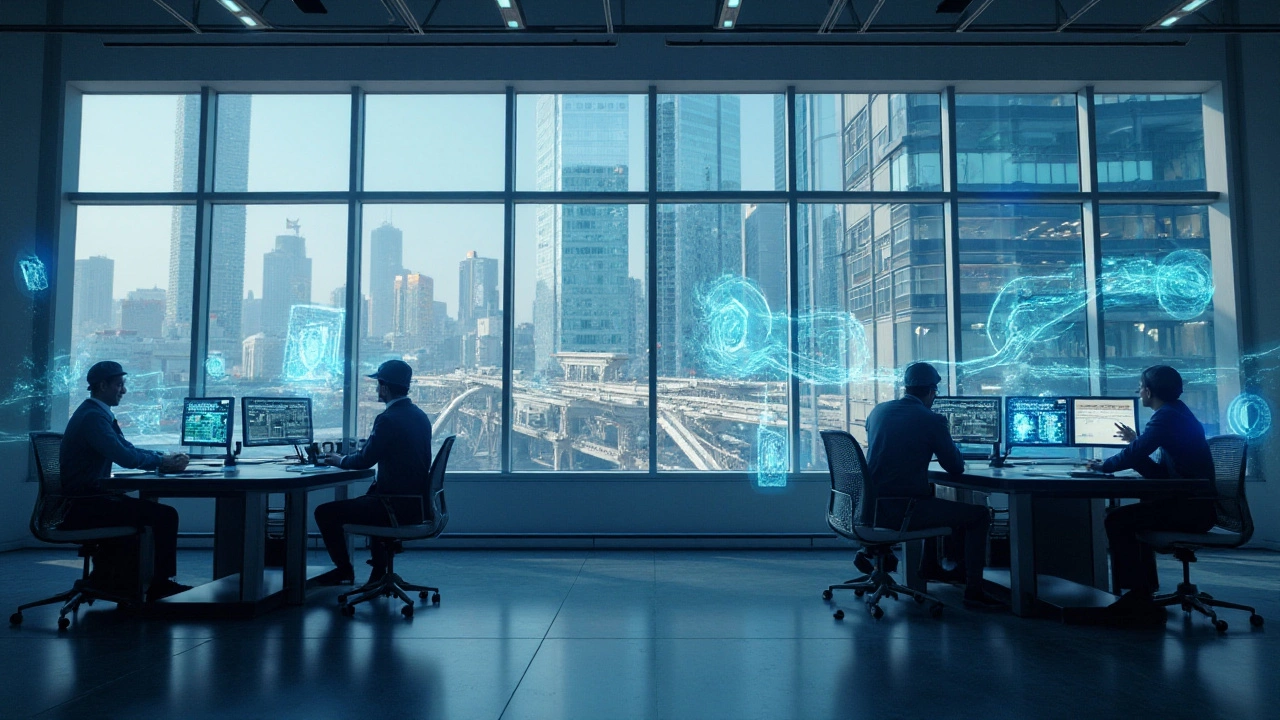
Будущее цифровых примеров в производстве
Цифровые технологии — это двигатель прогресса, и цифровой пример становится одной из ключевых составляющих этого движения, кардинально меняя производство. Ожидается, что в ближайшие годы эти технологии позволят ещё шире интегрировать виртуальные модели в реальные производственные процессы. Представьте себе завод, способный заранее спрогнозировать каждую деталь работы машин, оценить износ оборудования и предсказать необходимость его замены задолго до того, как произойдет поломка. Это будущее, где цифровые примеры становятся неотъемлемой частью каждого этапа производства, от проектирования до сбора данных работающих механизмов.
На практике это означает, что более крупные компании начнут инвестировать в создание цифровых систем слежения за производством, постоянно совершенствуя их алгоритмы. Это позволит не только минимизировать издержки, но и обеспечить невероятную гибкость в условиях постоянно меняющегося рынка. По данным McKinsey, применение цифровых технологий в производстве может повысить эффективность использования оборудования на 20% и снизить эксплуатационные затраты на 15%.
"Интеграция цифровых примеров создаст новый уровень интеллектуальной работы в производственных цехах, повышая отзывчивость на изменение внешних факторов", — отмечает исследователь Мартин Хеллман, специалист по цифровой трансформации.
Впереди ещё много вызовов, связанных с адаптацией сотрудников к новым возможностям и внедрением их в корпоративные культуры компаний. Тем не менее, суммарные затраты на такие трансформации с лихвой окупятся за счет повышения производительности. Уже сейчас на рынке появляются компании, которые готовы полностью посвящать себя разработке таких решений, предлагая гибкие программные продукты, создающие комплексные аналоги производственных процессов.
Роль искусственного интеллекта и машинного обучения
Искусственный интеллект (ИИ) и машинное обучение (МО) играют не последнюю роль в будущем цифровых примеров. Эти технологии могут анализировать огромные массивы данных в реальном времени, что раньше было невозможно. Исследования компаний Microsoft и Google показывают, что интеграция ИИ в производство снижает вероятность ошибок на 30%, а время, затрачиваемое на анализ данных, сокращается с недель до нескольких часов.
- Автоматизация мониторинга: Постоянный анализ данных даёт возможность автоматически определять сбои и устранять их.
- Улучшение логистики: Оптимизация поставок позволяет минимизировать задержки и избежать перегрузок.
- Предсказание спроса: Изучение моделей покупательского поведения для более точного прогнозирования будущих заказов.
На горизонте технологий виднеется нечто большее — постепенное слияние физического и цифрового миров. Да, цифровые примеры уже сейчас могут перенастроить производство в зависимости от полученных прогнозов, обеспечивая продукцию более высоким качеством. Но это только начальная стадия их развития.
Оставить комментарий