Заводы сейчас уже не выглядят как филиалы фильмов про старый Советский Союз. Автоматизация, 3D-печать, роботы — всё это не просто модные разговоры, а часть реальной жизни любого современного производства. Если кто-то считает, что инновации — штука далекая и" игрушка для миллионеров", тут же ошибается. Новые технологии становятся доступнее, и вопрос уже не "стоит ли внедрять", а "как не опоздать".
Например, 3D-принтер из моего детства больше напоминал девайс из фантастики, а сейчас — инструмент, который реально экономит производителям десятки миллионов. Одна крупная машиностроительная компания в Екатеринбурге наладила выпуск запасных частей через 3D-печать и сократила логистику с месяцев до дней. Это конкретная выгода, а не просто красивая история для презентации.
- 3D-печать в машиностроении: где это уже работает
- Автоматизация и роботы: мифы и реальность
- Цифровые двойники: зачем их создают
- Экологичные технологии и сокращение отходов
- Умное оборудование: как меньше тратить и больше зарабатывать
- Советы для заводов: как не отстать и не разориться
3D-печать в машиностроении: где это уже работает
Когда слышишь про 3D-печать в машиностроении, у многих до сих пор в голове картинки игрушек или каких-то прототипов из пластика. На деле всё давно ушло дальше. Пример — КАМАЗ: там с 2023 года часть нестандартных деталей и крепежа изготавливают прямо на заводе с помощью печати из металлопорошков. Это ускоряет ремонт и уменьшает простои техники на 40%.
Во всем мире такие технологии уже являются ежедневной практикой. Например, немецкий Siemens печатает сложные элементы для газовых турбин. Та же технология работает в авиации — General Electric используют 3D-принтеры для изготовления форсунок для двигателей. Их детали легкие, прочные, а цена — ниже классической металлообработки. В России активно печатают детали для сельхозтехники — это спасает аграриев, когда оригинальные запчасти ждать долго.
Вот где особенно ясно, что 3D-печать — не просто хайп:
- Запасные части для станков и конвейеров. Можно быстро «выключить форс-мажор», не дожидаясь доставки из другой страны.
- Модернизация старого оборудования. Производитель уже не выпускает деталь? Её печатают по цифрам, с доработками под текущие нужды.
- Производство опытных образцов. Не надо тратить недели на изготовление пресса — напечатал, проверил, подогнал конструкцию под себя.
Для машиностроительных компаний это реальный способ экономить, а иногда и просто выживать. По данным Ассоциации аддитивных технологий, к 2024 году каждая третья крупная компания в России использует хотя бы одну 3D-печать в производственной цепочке. Ниже — простая таблица, где видно, как меняются показатели:
Сфера применения | Экономия по времени | Снижение затрат |
---|---|---|
Ремонтные работы | до 80% | до 50% |
Производство деталей на заказ | до 70% | до 35% |
Важно: даже небольшие заводы берут эту технологию на вооружение. Главное — грамотно оценить, какие детали реально удобнее и дешевле напечатать, а что проще закупать старым способом. Два года назад сам видел, как небольшой цех в Челябинске вышел из ситуации с поломкой уникального пресса, просто напечатав нужную пластину — экономия составила двести тысяч рублей. Вот она, живая инновация.
Автоматизация и роботы: мифы и реальность
Часто кажется, что если на заводе появились роботы, то люди окажутся без работы. Но вот факт: по данным Ассоциации промышленной автоматизации России, в 2024 году внедрение роботов увеличило общую производительность предприятий на 27%. При этом потребность в квалифицированных сотрудниках только выросла. Роботы отлично справляются с рутиной, но для обслуживания новых систем нужны люди — инженеры, айтишники, операторы.
Многие считают, что автоматизация и умные машины — это невероятно дорого и подходят только большим корпорациям. Но массовое распространение и падение цен на компоненты сделали современные технологии доступными не только для гигантов, но и для малого бизнеса. Пример: производитель автозапчастей из Ижевска вложил около 5 млн рублей в простейших коллаборативных роботов и уже за год отбил вложения, снизив количество брака почти на 50%.
Важно понимать: автоматизация — это не только про конвейер и роборуки. Сюда входит всё: от обычных датчиков, которые следят за температурой или давлением, до сложных систем, которые собирают данные в облаке и показывают результаты на смартфоне мастера.
Вот несколько самых устойчивых мифов про инновации в машиностроении, которые пора забыть:
- Роботы — это угроза рабочим местам. На деле появляются новые вакансии с более высокой оплатой и требованием новых навыков.
- Автоматизация — это космос по цене. Если грамотно выбрать задачи для перехода на "умную" технику, инвестиции окупаются быстрее, чем кажется.
- Всё решают западные технологии. Российские заводы уже используют локальные решения и легко их адаптируют под любую задачу.
«Наши рабочие боялись, что роботы их заменят. На деле многие прошли обучение и получили новую профессию буквально за несколько месяцев. Сегодня основной доход приносят именно новые цифровые процессы» — говорит Иван Брагин, технический директор производственного холдинга в Тольятти.
Ещё одна реальная история: на одном из заводов под Нижним Новгородом внедрение интеллектуальной системы контроля качества позволило снизить простои оборудования на 40%. Так, люди меньше занятого времени тратят на устранение аварий, зато больше участвуют в улучшении процессов и учатся работать с современными технологиями.
Год | Доля автоматизированных заводов РФ | Среднее время простоя (часы/год) |
---|---|---|
2021 | 36% | 185 |
2023 | 51% | 112 |
Автоматизация — не фантастика и не повод для паники. Если грамотно подойти к внедрению, выигрывают все: и бизнес, и сотрудники, и клиенты.
Цифровые двойники: зачем их создают
Про машиностроение всё больше говорят не только заводские работяги и инженеры, но и айтишники. Одна из последних фишек — цифровой двойник. Это не просто 3D-модель на компьютере, а цифровая копия реального станка, целого цеха или даже производства, с которой можно делать что угодно: тестировать новые детали, анализировать поломки, просчитывать ремонты или перестройки — всё не вставая из-за стола.
Зачем вообще нужны эти двойники? Ответ очень простой — они экономят время, деньги и нервы. Любая ошибка в реальном цехе стоит дорого. С двойником можно ещё на компе увидеть косяк, проверить новое решение или прогнать нестандартную ситуацию.
Вот реальный кейс: в конце 2023 года на заводе «Кировский завод» внедрили цифровых двойников для парка промышленных станков. Через полгода удалось сократить внеплановые остановки на 18%. Люди просто заранее понимали, где и когда возможен сбой, и не ждали, пока оборудование загнётся окончательно.
Что помогает сделать цифровой двойник?
- Тестировать оборудование без риска сломать что-то дорогое
- Находить слабые места конструкции — ещё до запуска в реальное производство
- Планировать ремонты и обслуживание точнее, без аврала и спешки
- Обучать новых сотрудников на виртуальном производстве — реально безопасно и удобно
У крупных производителей, вроде Siemens или КАМАЗ, цифровые двойники используются уже несколько лет. Они планируют с помощью них даже целые заводы — меняют логистику, компоновку рабочих мест и маршруты техники. Всё сначала моделируют виртуально, чтобы не сливать деньги на ошибки в реальности. Кстати, по данным аналитиков, компании, которые внедряют такие технологии, сокращают издержки на обслуживание на 10-20%.
Год | Производители, внедрившие двойников | Снижение простоев (%) |
---|---|---|
2023 | Кировский завод | 18 |
2022 | КАМАЗ | 13 |
2021 | Siemens | 15 |
Для малого бизнеса всё это тоже становится доступно. Сейчас есть отечественные IT-компании, которые легко делают цифровые двойники для оборудования за небольшие деньги. Реальные выгоды уже никто не будет отрицать: если хочешь выжить в производстве — пора не бояться пробовать такие решения.
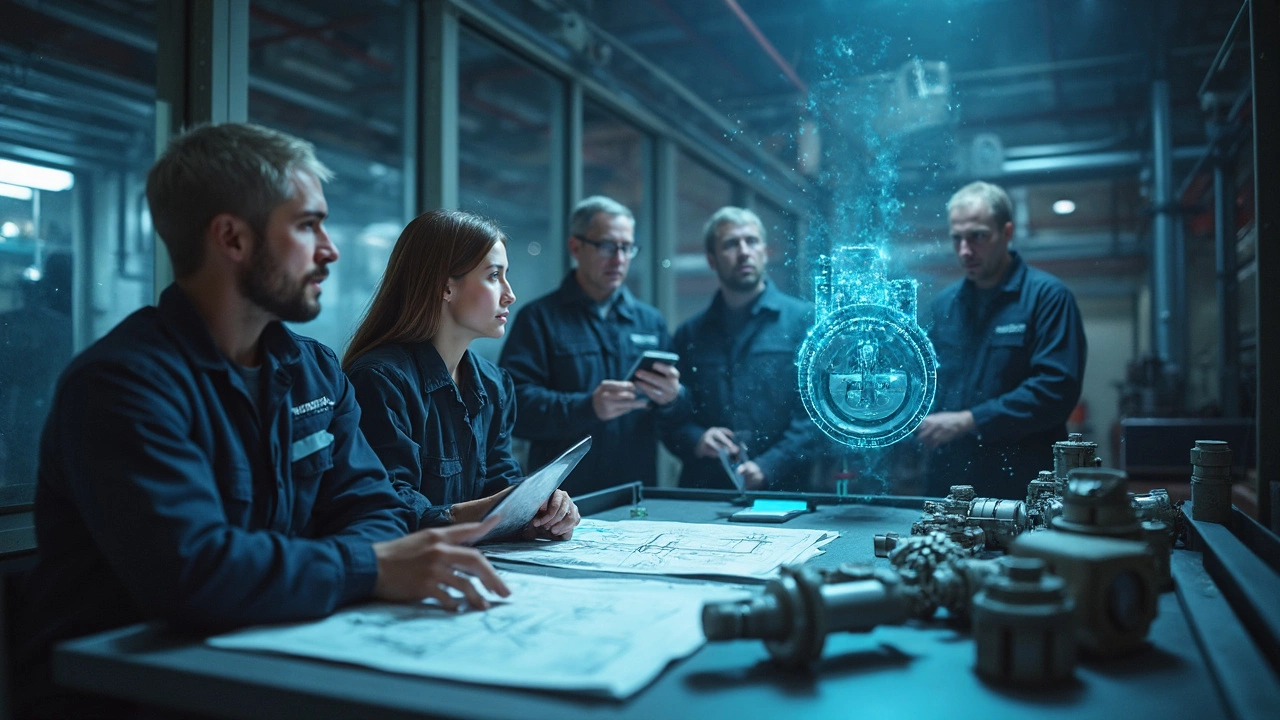
Экологичные технологии и сокращение отходов
Экология уже не только про сортировку отходов дома. Сегодня машиностроение смотрит в сторону максимального уменьшения вреда природе. И это не для галочки — на многих европейских рынках без «зелёных» сертификатов вообще нечего делать.
Например, одно из главных направлений — повторное использование производственных отходов. Многие заводы внедряют системы сбора и переработки стружки и шлама. Это позволяет экономить материалы — например, сталь или алюминий возвращают обратно в производство, а не вывозят на свалку.
Вот яркий пример: на петербургском предприятии в 2023 году поставили установку по фильтрации воды, использованной при резке металла. Экономия воды достигла почти 60%. Плюс меньше химии уходит в канализацию.
«Сегодня любые инвестиции в бережливые и экологичные технологии быстро возвращаются. Для нашего завода снижение отходов — это не только забота об окружающей среде, но и о прибыли», — отмечает Михаил Блинников, технический директор «СеверСтальМаш».
Что ещё активно внедряют в инновациях и производстве:
- используют станки с функцией энергосбережения (некоторые модели снижают расход электричества почти в два раза);
- заменяют масляные смазки на водорастворимые;
- устанавливают отдельные линии для сортировки металлолома;
- вводят новые фильтры на выбросах для снижения пыли;
- автоматизируют учёт и мониторинг отходов, чтобы видеть и сразу сокращать потери.
Если говорить про современные технологии, то аддитивные (3D) технологии ещё помогают снизить количество брака — ведь деталь делается только один раз, по точному эскизу. Производство становится точнее, брак — реже.
Завод | Экономия материалов (%) | Снижение водопотребления (%) |
---|---|---|
УралМаш | 18 | — |
СеверСтальМаш | 15 | 60 |
ПитерТех | 12 | 25 |
В работе заводов теперь выигрывает тот, кто не только собирает меньше отходов, но и экономит на этом деньги. Это не мода — это прямая выгода и будущее всей индустрии.
Умное оборудование: как меньше тратить и больше зарабатывать
Теперь машиностроение движется в сторону полного контроля и автоматизации. «Умное» оборудование сразу видно по его возможностям: оно само следит за рабочим процессом, анализирует данные и даже предупреждает, когда что-то идет не так. Это не только модная игрушка — это способ экономить ресурсы и избегать лишних простоев.
На многих современных производствах стоят сенсоры, которые мгновенно сообщают, если станок начинает работать не так, как обычно. Простой пример: на одном заводе в Челябинске умные станки позволили снизить незапланированные поломки почти в два раза за год — только за счет мониторинга и быстрой реакции. Стоимость простоя одной линии там — 250 тысяч рублей в день. Почувствовали разницу?
Вот реальные плюсы перехода на такие технологии:
- Экономия времени — меньше простаев и простоев из-за неожиданных поломок.
- Современные технологии повышают качество: оборудование постоянно само себя калибрует.
- Расход материалов под контролем — система считает всё вплоть до грамма.
- Плановый ремонт заменяет аварийный — можно заранее понять, что износилось.
Можно даже увидеть цифры. В отчёте Ассоциации машиностроителей России за 2024 год указано:
Тип оборудования | Экономия на ремонте | Сокращение простоев |
---|---|---|
Обычное | до 5% | 3-4 дня/мес |
"Умное" | до 22% | менее 1 дня/мес |
Эксперт по производству Сергей Клепиков говорит:
"Сегодня главный ресурс — информация. Кто первым получил данные о работе оборудования, тот и выиграл. Реакция на сбой за минуту вместо часа — это прямые деньги."
Так что если думаете, что пора что-то менять, начните хотя бы с самого простого: поставьте датчики на критические точки, даже если у вас не суперсовременный завод. Цена вопроса минимальная, а отдача реально есть.
Советы для заводов: как не отстать и не разориться
Машиностроение – не та сфера, где можно позволить себе расслабиться. Инновации накатывают одна за другой, и если не пользоваться новыми технологиями, можно реально закрыть бизнес из-за неэффективности. Вот что я замечаю у знакомых руководителей: те, кто ставит ставку на обновление, выживают лучше.
Что конкретно можно сделать, чтобы не просто выживать, а зарабатывать?
- Инвестируйте в обучение персонала. Роботы и системы автоматизации – штуки стоящие, но если сотрудники их не понимают, толку мало. Самое простое – подписывать людей на курсы по современным технологиям производства, те же онлайн-программы условного Яндекса или Skillbox.
- Внедряйте цифровые двойники. Это не пустые слова. Например, на "Кировском заводе" за счет цифрового двойника снизили аварийность оборудования на 20%. Это огромная экономия на ремонтах и простоях.
- Оптимизируйте логистику. Большие склады устаревают. Компании, которые устанавливают автоматизированные системы складирования, реально сокращают потери и время переброски деталей с недель до часов.
- Не забывайте про экологию. Использование повторного сырья — уже не опция, а часто требование крупных заказчиков. Переход на оборудование, умеющее разделять отходы и экономить сырье, повышает шансы на тендерах.
- Считайте каждую копейку. Автоматизация, конечно, требует денег на старте. Но быстро окупается. На том же стапеле можно сэкономить тысячи человеко-часов в месяц.
Как говорили в исследовании "Инновации в российском машиностроении" (НИУ ВШЭ, 2023):
«Заводы, которые внедрили хотя бы одну цифровую технологию за последние три года, показывают рост производительности на 17-22% по сравнению с теми, кто стоит на месте».
И да, госпрограммы поддержки никуда не делись. Льготные кредиты, субсидии на закупку оборудования — этим важно пользоваться, чтобы внедрять инновации с минимальной финансовой нагрузкой.
Технология | Пример завода | Экономия или результат |
---|---|---|
3D-печать | Завод в Екатеринбурге | Сокращение сроков поставок с 5 недель до 4 дней |
Цифровой двойник | Кировский завод | Минус 20% аварий |
Автоматизация склада | Липецкий тракторный | Экономия 15 сотрудников, быстрый оборот комплектующих |
Смысл простой: пока кто-то спорит, нужны ли инновации в машиностроении, более расторопные соседи уже зарабатывают на новых технологиях и отвоёвывают рынок.
Оставить комментарий