Машиностроение на старте цифровой революции
Машиностроение всегда было основой промышленности. Раньше представьте себе обычный завод: гул станков, рабочие, замасленные детали, от бумажной документации отчаянно хочется спать. Но лет за десять всё изменилось: цифровые технологии зашли на территорию огромных цехов и старых станков, как айфон на старый кнопочный телефон. Уже сегодня большая часть процессов на развитых предприятиях, от диагностики до сборки, плотно связана с интернетом вещей (IoT), искусственным интеллектом и печатью деталей на 3D-принтерах. Цифровые технологии не просто «помогают», они создают новые бизнес-модели и целые отрасли внутри привычного машиностроения.
Как-то один известный российский завод по выпуску энергетического оборудования четыре года назад решил: пора цифровизироваться. Внедрили предиктивную диагностику на основе IoT-датчиков — каждая вибрация, каждое колебание температуры передаётся в общую систему мониторинга. Если деталь изнашивается раньше графика, система показывает это до того, как случится авария. Итог: завод сэкономил больше 70 миллионов рублей только на предотвращении простоев за первый год. Раньше сбои приводили к тому, что весь поток работ тормозился. Теперь всё работает как часы — естественно, если часы тоже на цифровых сенсорах.
Эти изменения неотделимы от роста автоматизации и потребности в обработке огромных массивов данных. У любого технолога сегодня экран почти как в фильме «Бегущий по лезвию»: на мониторах — тепловые карты завода, графики, отчеты, AI-подсказки. А без больших данных и машинного обучения такая визуализация невозможна: система обрабатывает тысячи сигналов в реальном времени, ищет отклонения, советует принять меры. Всё, чтобы машины служили дольше, продукция оставалась качественной, а потери минимальными.
Эксперты дают совет: цифровая трансформация не обязана идти масштабно и за один сезон. Часть предприятий начинает с одного цеха: проводят пилотные проекты на отдельном участке, считают выгоду. Если проект окупился — масштабируют на весь завод. Такой подход не просто снижает риски, а даёт реальное представление, где IT-решения приносят максимальную пользу и какие зоны требуют доработки.
Интернет вещей: глаза и уши современного завода
IoT — не модное слово из презентаций, а уже живая реальность для машиностроения. Маленькие датчики, похожие на фишки домино или «подслушивающие жучки», буквально вселяются в детали и оборудование. Их задача — непрерывно снимать показания: давление, температуру, уровень вибраций, потребление энергии. Все данные летят в облако, где системы аналитики круглосуточно отслеживают состояние техники.
Что это даёт реально? Например, заметили на одном из автоконцернов: раньше для контроля температуры смазки в прессах использовали точечные замеры. Из-за этого, когда температура скачет утром, но к вечеру нормализуется, проблема часто оставалась незаметной. Со временем из-за этого выходил из строя целый форматный пресс стоимостью под миллион евро. После установки IoT-датчиков инженеры постоянно получают свежие данные и могут вовремя подкорректировать параметры. В результате надёжность и предсказуемость стали почти идеальными, аварий стало в три раза меньше.
Для среднего или небольшого завода переход на IoT — не всегда означает капитальные вложения на миллионы. Начать можно с базового комплекта: поставить на пару узлов важные датчики, запустить сбор информации. Через полгода-год — подвести итоги: уменьшились ли простои, быстрее ли идет ремонт, снизились ли издержки? Если результат виден — подключают новые цеха, ещё больше расширяют возможности аналитики.
Широко используют IoT для энергоэффективности: в цехах отслеживают энергопотребление по сменам, тестируют режимы прогрева оборудования, замечают пики и «утечки» энергии. Иногда достаточно заменить несколько сверхпрожорливых электродвигателей — расход падает сразу на 30%. Как считают на одном из машиностроительных предприятий в Татарстане, система окупила себя всего за 6 месяцев.
Интересная особенность — IoT стал одним из драйверов перехода к сервисной модели. Не просто поставил станок и забыл, а предоставляешь сервис: следишь за оборудованием клиента удалённо, сообщаешь об отклонениях, помогая избежать крупных поломок. Вот она, та самая цифровая добавленная стоимость, о которой много говорят на форумах: теперь важно не только продать технику, но и сопровождать её достойно технологически.
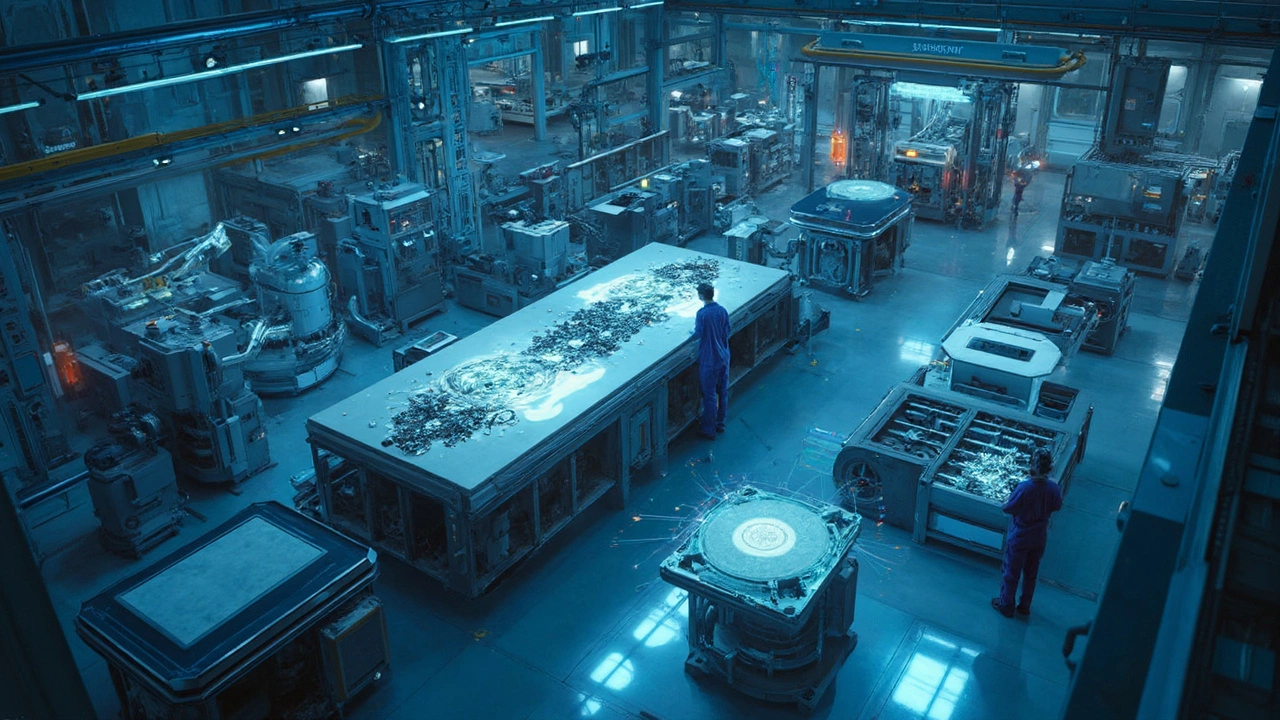
Искусственный интеллект: мозг новой индустрии
Без AI не обходится ни один разговор о современном производстве. Если IoT — это глаза и уши, то AI — мозг, который анализирует все данные и предлагает решения. Сегодня системы искусственного интеллекта умеют предсказывать срок службы деталей, рассчитывать идеальную траекторию роботы-манипулятора, даже распознают по характеру вибрации или звука, что станок требует обслуживания. То, что раньше было интуицией старого мастера, теперь передано нейронным сетям и алгоритмам.
Крутой кейс — завод по производству turbine генераторов: там AI анализирует в режиме реального времени работу каждого узла, выявляет малейшие отклонения от нормы. Если вращение генератора проходит не по графику, приходит сигнал оператору: «Вмешайтесь — возможна рассинхронизация!» Благодаря этому число аварийных простоев снизилось на 40%, а специалисты быстрее находят нестандартные сбои.
Ещё пример — система контроля качества сварки. Раньше технологи полагались только на опыт и визуальный контроль. Сейчас AI способен буквально увидеть тот дефект, который пропустил бы обычный глаз. Как делают: на выходе из линии камеры фиксируют сварные швы, искусственный интеллект моментально сравнивает с идеальным образцом. Отклонение — мгновенный сигнал. Ошибка не идёт дальше, риск выпуска брака снижается почти до нуля.
В отдельную категорию попадают цифровые двойники. Это виртуальные модели оборудования, которые используют для тестов и оптимизации — прямо на экране можно проверить, выдержит ли станок новую нагрузку или, скажем, поменять параметры сборки без риска порвать реальную железку. Одна компания на Урале за счёт внедрения цифрового двойника сократила время разработки нового продукта с трёх месяцев до двух недель!
AI сейчас всё чаще применяется для автоматизации снабжения: система сама заказывает необходимые детали на складе, анализируя графики потребления и прогнозируя пик производства. Человеческий фактор уходит на второй план, логистика становится точнее и быстрее.
Можно сказать, современные сферы развития производства и технологий неотделимы от AI и IoT. Об этом подробнее можно почитать здесь: как интеграция IT и машиностроения меняет саму экономику.
Аддитивные технологии: 3D-печать как точка роста
Пару лет назад 3D-печать казалась чем-то из фантастики: вроде бы игрушка для дизайнеров или прототипирования. Но сейчас на крупных машиностроительных предприятиях 3D-принтеры стоят наряду со станками, часто выступая «палочкой-выручалочкой» там, где стандартные методы буксуют. Аддитивные технологии позволяют создавать сложные формы без необходимости держать склад стандартных запчастей. От деталей для редукторов до корпусов электродвигателей — всё печатают буквально на месте, по нужным параметрам.
Конечно, речь не идёт о полной замене классических технологий. Но факт: ускорение запуска новых изделий, снижение затрат, отказ от хранения огромного склада малоиспользуемых запчастей — всё это аргументы в пользу расширения 3D-печати на производстве. Например, на одном предприятии в Самарской области благодаря печати металлических деталей сократили время на ремонт редких узлов двигателя в семь (!) раз, а складские издержки уменьшились почти на треть.
Сложно переоценить значение 3D-печати в мелкосерийном производстве — именно там, где каждая силовая установка или редуктор может быть уникальным. Но и крупные заводы всё чаще проектируют сложные пресс-формы и технологическую оснастку именно в цифровом виде, чтобы потом тут же напечатать нужную «деталь-штамп» к новой партии изделий.
Есть интересная закономерность: где внедряют аддитивные технологии в связке с IoT и AI, скорость обратной связи возрастает в разы. Скажем, искусственный интеллект анализирует реальные параметры эксплуатации детали, на основе этих данных меняют модель, тут же печатают доработанную версию — и отправляют в работу, не тратя недели на заказ, доставку и доработки.
Кроме того, 3D-принтеры помогают не только с ремонтом или прототипами, но и с серийным выпуском деталей с уникальными свойствами: сложные каналы охлаждения, интеграция датчиков внутрь корпуса детали, облегчённые конструкции — всё это легко реализуется только с помощью аддитивного производства.
Эксперты советуют: если предприятие задумывается, с чего стартовать внедрение 3D-печати, оптимально начать с «узких мест» — делать нестандартные детали либо оснастку для сборки и контроля. Через несколько месяцев результаты станут зримыми — отсутствие ожидания поставок, быстрые доработки, экономия на логистике.
Подытожим: цифровые технологии сегодня не просто инструмент модернизации машиностроения — это реальный драйвер нового роста, дающий шанс российской отрасли быть конкурентной как в стране, так и на мировом рынке. Главное — не бояться идти вперёд, пробовать, интегрироваться в цифровую экосистему. Именно так будущее и становится настоящим.
Оставить комментарий