Четыре пункта обеспечения качества — не абстрактные правила, а рабочий инструмент, который действительно спасает нервы и деньги. Особенно, если речь идёт о машиностроении: здесь любая ошибка может стоить не только прибыли, но и репутации компании.
Знаете, где чаще всего "выстреливает" брак? Не там, где его ожидаешь. Деталь вроде собрали отлично, протянул болт — и вся система завалилась, срок сорван, а начальство нервничает. Проблема в том, что кто-то пропустил хотя бы один из этих четырёх этапов: планирование, контроль, обеспечение и улучшение качества. Это как забыть пристегнуть ремень безопасности — ты можешь и не попасть в аварию, но если что-то случится, будет больно всем.
Не нужно влюбляться в бумажки ради бумажек — система должна работать на людей и для людей. По крайней мере, я за этим на заводах и гоняюсь: чем проще, тем полезнее для цеха и бригады. Дальше расскажу, как эти четыре пункта реально работают на практике и почему без них сегодня нельзя выпустить ни одну хорошую деталь.
- Зачем нужно управление качеством на заводе
- Планирование качества — первая голова дракона
- Контроль качества: как не пропустить брак
- Обеспечение качества: работа на упреждение
- Улучшение качества: вечный двигатель успеха
- Ошибки, которые ломали даже крупные производства
Зачем нужно управление качеством на заводе
Честно говоря, если на заводе нет нормального управления качеством — ждите проблем. Любое производство, особенно крупное, напоминает футбольную команду: пока каждый играет по правилам и не халтурит, всё работает. Как только начинаются сбои — мяч попадает в собственные ворота. Один пример: на российском рынке машиностроения примерно 15% деталей отправляется на доработку или брак при слабом контроле качества (данные АСИ за 2023 год).
Чтобы такого не было, на заводе должна работать система, где каждый точно знает:
- какой стандарт нужно соблюдать;
- чем занимается каждый сотрудник;
- как и когда выявлять косяки;
- кто и что делает, если случается ошибка.
Если этого нет — все эти процессы начинают путаться, а качество падает. По статистике, компании, внедрившие системные подходы к качеству, в среднем снижают расходы на исправление брака на 25% и получают меньше возвратов от заказчика. Деньги и нервы сохранены, клиенты довольны.
Вот небольшой пример в цифрах для машиностроения:
Показатель | Без системы качества | С внедрением контроля |
---|---|---|
Процент брака, % | 15 | 5 |
Срок поставки (дней) | +7 | 0 |
Возвраты клиентов, шт./мес. | 30 | 8 |
Всё по-честному: если нет управления, завод буксует. Когда всё налажено, экономишь ресурсы и не краснеешь перед клиентом. Поэтому для меня главный вопрос — не "нужно ли", а "почему кто-то до сих пор этого не делает".
Планирование качества — первая голова дракона
Вот откуда всё начинается. Если на старте ошибиться с планом, никакой контроль не спасёт от косяков. В машиностроении планирование качества — не просто документ, а конкретный протокол, как будут идти работы, что и кто должен делать, и по каким требованиям потом будет сверяться результат.
Планирование качества охватывает сразу несколько деталей:
- Определяют, какие стандарты и нормативы обязательны — российские (ГОСТ, ОСТ) или международные (например, ISO 9001).
- Устанавливают, какие материалы и комплектующие можно применять. Например, в авиации без паспорта качества детали не примут даже бесплатно.
- Делают маршрутные карты и чек-листы для каждого цеха: что делать, кто отвечает, когда и как должна идти проверка.
- Согласуют с отделом логистики сроки поставки, чтобы не было простоев из-за того, что гайки приехали с опозданием.
Средняя продолжительность этапа планирования в крупном авиазаводе — 2-4 недели, а на средних предприятиях хватает и 5-7 дней. Если тянут резину — потом всё производство идёт "криво".
Этап | Обычное время (дни) | Риски при пропуске |
---|---|---|
Выбор стандартов | 1–2 | Несоответствие продукции, штрафы |
План по материалам | 2–3 | Просроченные поставки, лишние траты |
Чек-листы и карты | 1–2 | Ошибки при сборке, путаница в процессах |
Утверждение сроков | 1–2 | Срывы выпуска, простои |
Всё делается заранее, чтобы каждый на своём месте понимал: "Мой фронт работы — вот этот, правила такие, ответственность — вот она". Честно говоря, лучше час потратить на хороший план, чем неделю потом разгребать брак и пинать поставщиков.
Даже качество тут не самоцель: если продумаешь всё заранее, сэкономишь деньги и нервы всей бригаде. В моей практике на одном заводе забыли согласовать формат сварочного шва — потом на тысячи изделий пришлось в спешке переделывать, теряя время и деньги. Лучше планировать, чем латать проблемы.
Контроль качества: как не пропустить брак
Контроль качества — сердце всего процесса. Проморгали тут брак — всю цепочку испортили, а иногда и отношения с клиентом потеряли. В машиностроении даже маленькая ошибка ведёт к большим затратам. Например, 80% рекламаций можно было бы избежать, если вовремя заметить несоответствие на ранних этапах.
Что реально работает? Разделять виды контроля и не надеяться, что «дядя Вася из ОТК» всё выловит. Нормальная система включает:
- Входной контроль материалов — браковать уже здесь всё, что не по стандарту.
- Операционный контроль: на каждом этапе сборки или обработки не лениться проверять ключевые параметры деталей.
- Приёмочный контроль — финальная, беспощадная фильтрация изделий перед отправкой на склад или заказчику.
«Лучший контроль качества — это тот, который не даёт дефектной детали стать частью следующего изделия. Всё остальное — исправление чужих ошибок за свой счёт», — говорил Константин Косырев, эксперт Ассоциации машиностроителей России.
Цифры никогда не врут, особенно на производстве:
Тип контроля | Частота отклонений, % | Вносимый вклад в выявление брака |
---|---|---|
Входной | 3 | Выявляет 12% общего брака |
Операционный | 7 | «Ловит» 60% проблемных деталей |
Приёмочный | 2 | Спасает от 28% претензий |
Чем проще маршрут, тем лучше всё контролируется. Привязывать контроль к человеку — плохая практика: лучше использовать чек-листы или автоматические приборы, особенно для сложных операций. Кстати, в машиностроении автоматический контроль на линии сократил задержки от брака почти на 40% у крупных игроков. На любой проводке экономить не стоит — дешевле вложиться один раз, чем потом перестраивать всю партию.
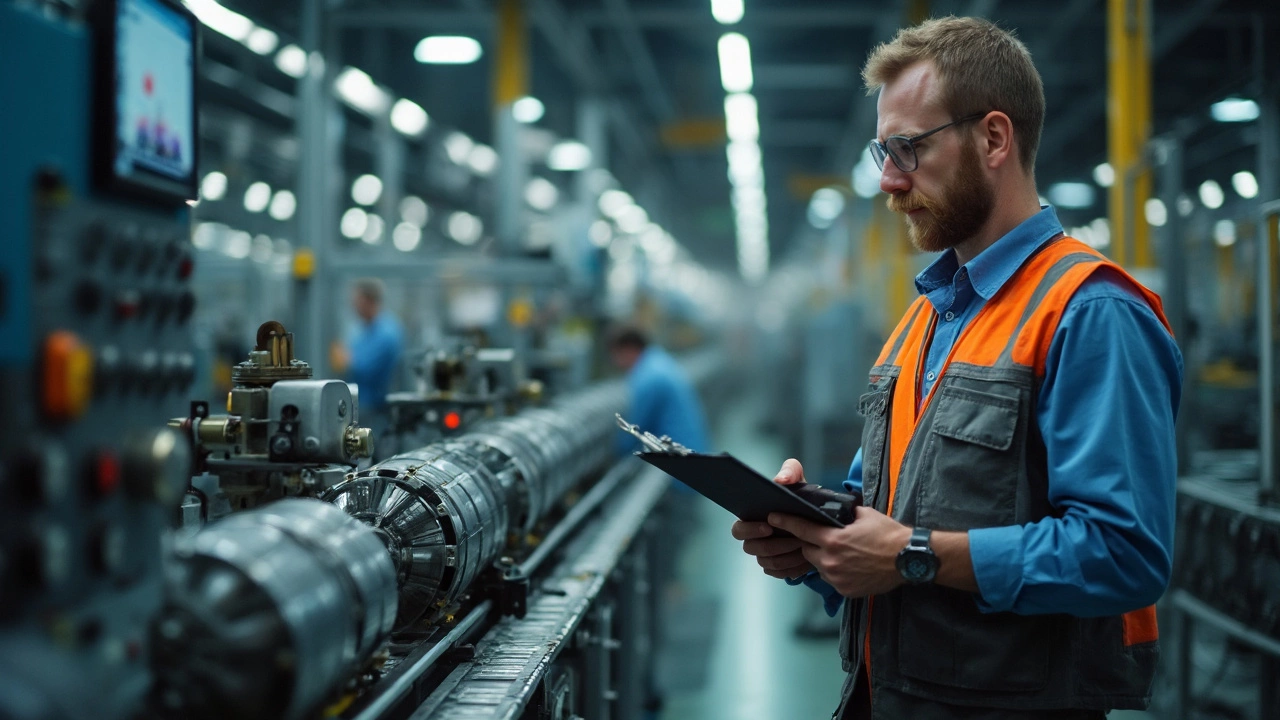
Обеспечение качества: работа на упреждение
Самое интересное в обеспечении качества — это работа на опережение, когда ты заранее ловишь ошибки, а не устраняешь последствия. Это и есть стратегия, которая отличает сильное производство от беготни с лампочками после аварии. В машиностроении без этого никак: детали дорогие, партии большие, ставка на надёжность всегда высокая.
Что реально значит обеспечение качества? Это не только контроль готового изделия, а и подготовка процессов, людей и материалов так, чтобы брак просто не пролезал. Вот тут пригодится чёткая документация, продуманные стандарты, постоянное обучение мастеров и проверенные поставщики. Всё работает проще, если цепочка выглядит так:
- Перед запуском партии проверяют оборудование по чек-листу. На многих заводах механики расписываются за исправность каждой единицы — прямо в журнале. Если где-то недокрут, его увидят до старта.
- Для новых деталей проводят пробный выпуск и собирают обратную связь от бригады. Технолог вместе с рабочими оценивает, понятно ли ТЗ, хватает ли инструментов, есть ли непредвиденные моменты.
- Используют входной контроль материалов — прежде чем закидывать сырьё в станки, лаборатория берёт пробы и сверяет их с нормой. Это поймать подделку или сырьё не того качества.
- Все изменения в техпроцессе обязательно согласуются с инженерами качества. Есть даже правило: без подписи специалиста на новой карте запуск невозможен.
Казалось бы, всё просто. Но если даже один пункт выпадает — начинается "эффект домино": проблема обнаружится уже на самом выпуске или у клиента. Иногда один неверный допуск на чертеже превращает десятки деталей в металлолом. Проще сделать сразу "под страховкой" — сработать качество на упреждение.
Совет из жизни: если появились повторяющиеся дефекты, не спеши искать виновного среди рабочих. Чаще всего причина — в процессе или в сырье. Тот же пример с автоматами: если часто сбивается настройка, обычно заводят отдельный журнал с причинами и реально сокращают простои. Всё фиксировать — и время, и вероятность повтора. Чем раньше найдёте "тонкое место", тем реже будете чинить авралы.
Улучшение качества: вечный двигатель успеха
Вот тут кроется настоящее топливо для роста. Даже если на заводе всё чётко, без постоянного улучшения можно быстро скатиться в повторяющиеся ошибки. В машиностроении конкуренция бешеная, а срок возврата к себе клиента из-за плохой детали может составить годы.
Улучшением качества нужно заниматься каждый день, а не только во время больших проверок. Это и есть путь к реальному снижению брака. Один мой знакомый начальник цеха рассказывал, что добился уменьшения рекламаций в три раза, когда перевёл бригаду на обсуждение ошибок каждую смену — без криков и штрафов, только практика "давайте улучшать вместе".
Что работает лучше всего:
- Регулярная обратная связь от сотрудников прямо с линии.
- Применение метода PDCA (Plan-Do-Check-Act) — простой цикл, который позволяет не погрязнуть в волоките и медленных корректировках.
- Анализ причин брака по системе "5 почему" — докапываемся до корня, а не затыкаем дыру.
- Мозговые штурмы раз в неделю буквально спасают от однотипных поломок оборудования.
В современных цехах автоматизация внесла свои коррективы. По данным Росстандарта, предприятия, внедрившие цифровой учёт дефектов и автоматизированные участки контроля, сокращают число брака в среднем на 27%. Это не значение "от балды", цифра из официального промышленного отчёта за 2023 год:
Год | Автоматизация | Среднее снижение брака (%) |
---|---|---|
2021 | Без автоматизации | — |
2023 | С автоматизацией | 27 |
Не забывайте вовлекать всю команду. Неважно, кто заметил слабое место в процессе — техник, наладчик или новичок. Лучшие решения рождаются без бюрократии: короткая встреча, реальный пример, понятный план. И помните, качество — это всегда дело всех на производстве.
Ошибки, которые ломали даже крупные производства
Когда смотришь на огромные заводы, кажется, что у них всё под контролем. А на деле срывы подряд — не редкость, даже у таких гигантов как АвтоВАЗ или Boeing. Обычно всё начинается с банального — кто-то решил сэкономить на грамотном контроле качества или не до конца продумал этап планирования. А потом одна мелкая ошибка превращается в лавину проблем.
Вспомним аварию Boeing 737 MAX. Оказалось, что сбои возникли из-за не до конца проверенной системы управления MCAS и недостаточного тестирования в условиях реальных полётов. В итоге компания потеряла миллиарды, временно остановила производство и была вынуждена переписывать процедуры по контролю и обучению персонала. Всё из-за того, что кто-то пропустил важные этапы проверки качества разработки программного обеспечения и не предусмотрел риски на старте.
На заводе АвтоВАЗ в начале 2000-х регулярно ловили брак уже на финальных этапах сборки. Причиной стали устаревшие стандарты контроля, когда каждый цех прикрывал свой "почерк", а о внедрении бережливого производства тогда только начинали задумываться. В результате, машины отправляли на рынок с мелкими, но массовыми дефектами, за что пришлось платить отказы клиентов и репутационные потери.
Вот типичные ошибки, которые срабатывают как ловушка и у гигантов, и у небольших предприятий:
- Переоценка своего оборудования — "Старый станок ещё потянет", а детали потом идут под обрез.
- Слабый ввод новых сотрудников, отсутствие наставничества и проверки практических навыков.
- Срезание этапов — "Успеем позже проверить качество целиком", а потом уже поздно что-то исправлять.
- Игнорирование сигналов с участка, когда рабочие реально видят, что процесс сбоит, но не могут пробиться к начальству.
Ошибка | Последствия | Пример из практики |
---|---|---|
Экономия на обучении | Рост брака до 10-20% | Снятие с продаж целых линеек кузовных деталей АвтоВАЗ, 2003 |
Устаревшие стандарты контроля | Снижение качества изделий, рекламации до 15% от партии | Начало 2000-х, оборонные заводы России |
Неполный аудит новых линий | Остановка производства, переработка за собственный счёт | Boeing 737 MAX, 2019 |
Мой совет — не думайте, что проблемы гибнут на входе в цех. Всё начинается с элементарного: внимание к деталям и честная обратная связь между инженерией и производством. Есть вопросы про качество — разбирайтесь сразу, а не "когда появится время". Экономия на ошибках — всегда проигрыш.
Оставить комментарий